Vigilance on Refrigerants
July 2024by Brendan Kavanagh
It’s an exciting time to be working on building decarbonization in Massachusetts. Aggressive climate policy coupled with rapid technological advances and growing public awareness have combined to accelerate progress towards achieving net zero carbon by 2050. Of course, many uncertainties, obstacles and potential pitfalls remain. One potential pitfall, which building practitioners and homeowners are uniquely positioned to influence, is refrigerant leakage.
Almost all refrigerants used in residential heat pumps are very potent global warming agents if they get into the atmosphere. If a whole home heat pump system installed today were to lose enough refrigerant to shut down, the refrigerant leakage could wipe out more than a year’s worth of the carbon emissions saved by converting to heat pumps.
The most common heat pump refrigerant in recent years has been R-410a, which over 20 years has a global warming potential (GWP20) 4,705 times greater than carbon dioxide. Before R-410a the most common residential refrigerant was R-22, which has a GWP20 5,610 times greater than CO2. R-22 also had a high ozone depletion potential, so the switch to R-410a was an improvement but not a permanent solution.
We are just now starting to phase out R-410a. The refrigerants poised to replace R-410a are R-32 with a GWP20 of 2,620 and R-454B with a GWP20 of 1,806. While these lower GWP refrigerants are a move in the right direction, a fast-moving industry wide transition like this will likely come with initial growing pains and increased costs.
Fortunately, preventing refrigerant leakage is at least conceptually simple: keep refrigerants inside our systems and out of the atmosphere. Refrigerants aren’t cheap, and systems that lose refrigerant eventually stop working. Climate impacts aside, it’s in homeowners’ and installers’ best interests to minimize refrigerant leakage. By following best practices, refrigerants can be contained and recycled many times over, allowing heat pumps to achieve the carbon emission reductions we are counting on.
So, let’s talk about the current landscape of refrigerants and what we can do to ensure they work for and not against us.
Where would I find refrigerants in my house?
The original home heat pump systems are refrigerators, which are assembled and charged (filled up) with refrigerant in a factory. Other factory charged systems include window air conditioners, heat pump water heaters, and condensing heat pump dryers. Such systems are less likely to leak than heat pumps and central air conditioners, which are assembled and charged on job sites. While it is difficult to quantify the increased risk, some studies indicate that the average annual leakage rate of field charged equipment ranges from 1-10% and factory charged equipment is lower ranging from 1- 6%.
When and how do refrigerants leak?
The most common time for refrigerants to escape into the atmosphere is at end of life - whether it’s because the homeowners don't know that the refrigerant needs to be recovered before disposal, or the recovery and recycling is poorly done. Factory charged systems can be dropped off at local recovery and recycling facilities. In some municipalities you can arrange for pickup at your home, possibly for a small fee.
Refrigerants in split systems must be recovered in place before the equipment is disassembled and removed. While the process of using a recovery machine and tank is well established in the industry, it takes more time and equipment than just venting the refrigerant to atmosphere so it unfortunately isn’t always done.
The next most common leakage risk occurs during on-site charging. It is best practice to test all piping for leaks before charging, but this too isn’t always done. HVAC installers who are under pressure to complete their work quickly may skimp on these tests. Common leakage points include poorly made connections or piping components that got damaged. If a leak is big enough the system will stop working soon after startup, whereas a system with a smaller leak will slowly operate less effectively until it shuts down. In all cases, it’s far more difficult to find and fix a leak after a system is full of refrigerant, so it is crucial that installers test before charging.
Are there other ways for systems to develop leaks?
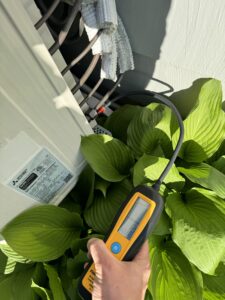
Refrigerant leak detector checking connection points on a faulty heat pump system.
Leaks can also occur during the operation phase of the equipment through no fault of the installers. This tends to happen a few years afterthe system is installed and often starts out slow before accelerating. The most common placefor this to occur is at the interior coil, often referred to as the “evaporator” coil. However, it can also happen along the line sets or at the outdoor coil, often called the “condenser”.
This type of leak is particularly challenging to address. The system might be out of warranty, or the installer might no longer be in business. Technicians often can’t diagnose and repair a leak during a single visit and might add refrigerant to the leaking system to keep it operating until they come back. Technicians might also advise homeowners against trying to fix the leak, and instead recommend a full replacement. If homeowners aren’t up for that, it’s not uncommon for technicians to repeatedly add refrigerant, sometimes for years. This happens so often it’s known as a “gas and go” and can result in massive amounts of refrigerant being released into the atmosphere over time.
What can be done?
For starters HVAC designers and installers should take refrigerant leakage seriously. Installers need to properly test systems before startup and have the expertise to find and fix leaks. Designers should advocate for good insulation and air sealing practices so they can specify smaller heat pumps with less total refrigerant along with mechanical solutions that can further reduce total refrigerant and/or use lower GWP refrigerants. Homeowners should have some backup heating or cooling – such as electric space heaters or a wood stove, and a couple of low-cost window AC units. Finally, the easiest and most important thing is to recover and recycle all refrigerant before disposal.
What does all this mean for my house?
In our opinion, heat pumps are the most affordable, efficient and low-carbon heating and cooling technology currently available. When it is time to replace your current system, we believe that a heat pump will almost certainly be your best choice – especially if you plan ahead.
When your existing equipment is serviced, ask the technician how much life they think your system has. Start preparing a replacement plan well ahead of time so that you are ready to execute it before your equipment dies. If you haven’t recently had a Mass Save assessment, see if you can schedule one. This will give you access to utility incentives for heat pumps and ensure you have implemented weatherization measures available through Mass Save. Consider making envelope improvements that go beyond Mass Save measures. We can help with this, or you could work directly with an insulator that does market rate insulation work as well as Mass Save insulation. If your current HVAC company installs heat pumps, talk to them as well as to friends and neighbors who have installed heat pumps. Be sure to ask good questions when you talk to HVAC installers so that you consider more than just price when deciding who to hire.
Meanwhile, here at Byggmeister, we will remain vigilant on refrigerants so that we can continue to help our clients decarbonize their homes with confidence.